Understanding Surface Finish: Ra vs. RMS for Metal Fabricators
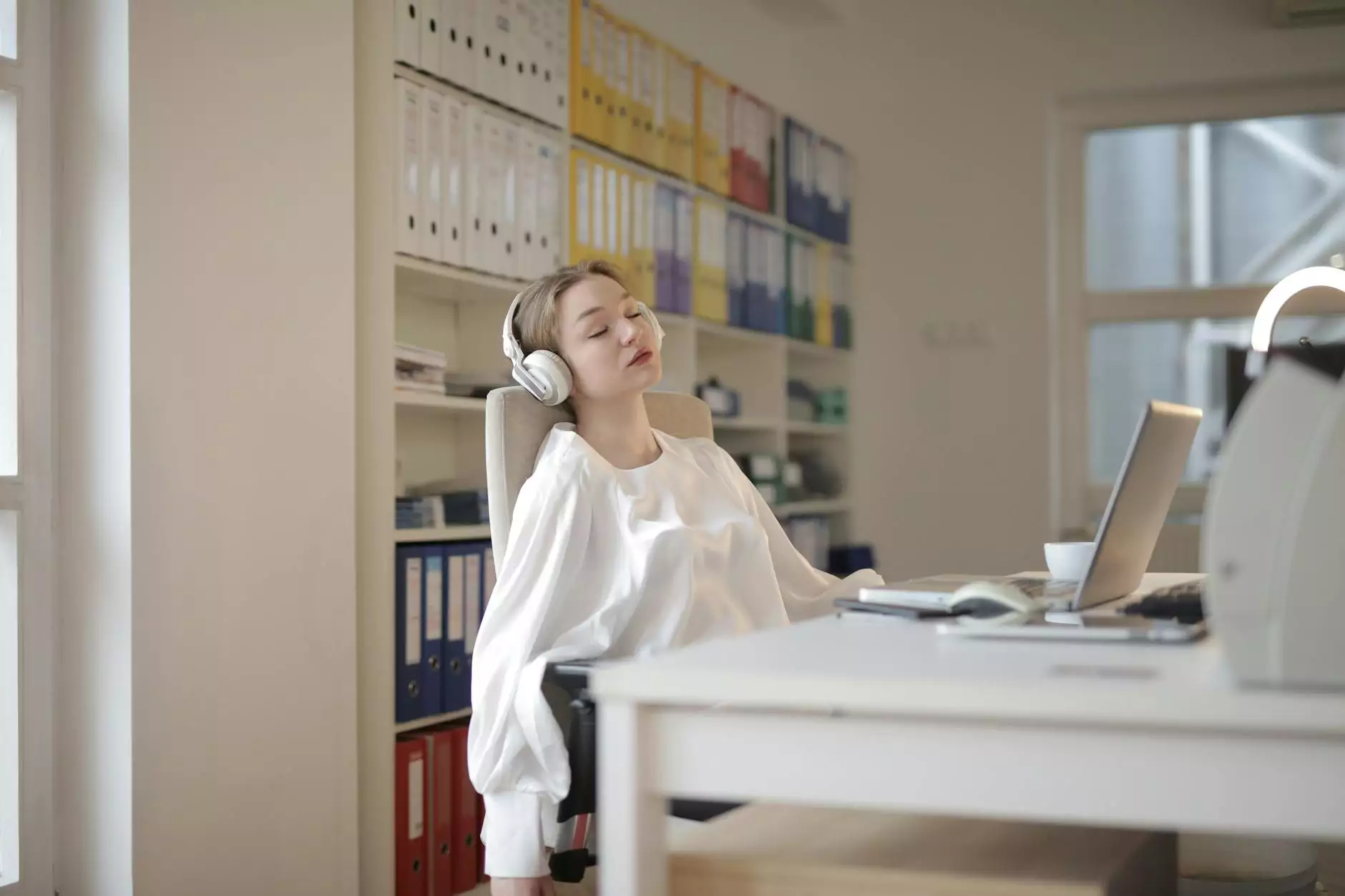
In the world of metal fabrication, surface finish plays a critical role in determining the quality and performance of a finished product. Among the various metrics used to quantify surface finish, Ra (Roughness Average) and RMS (Root Mean Square) are the most widely discussed. This article delves into the distinct characteristics, applications, and implications of surface finish Ra vs. RMS, equipping manufacturers with the knowledge to make informed decisions about their processes and products.
What is Surface Finish?
Surface finish refers to the texture or smoothness of a surface after fabrication. It is an essential factor that influences several performance attributes, including:
- Aesthetic appearance
- Wear resistance
- Corrosion resistance
- Fatigue strength
- Friction characteristics
Achieving the desired surface finish is crucial in various industries, from aerospace to automotive. The metrics used to measure surface finish, particularly Ra and RMS, provide insight into how effectively these characteristics are achieved.
Defining Ra and RMS
Surface Finish Ra (Roughness Average)
Ra, or Roughness Average, is a critical parameter in assessing surface finish. It is defined as the arithmetic average of absolute values of the surface roughness profile measured over a specified length. The Ra value is expressed in microinches or micrometers. In simpler terms, Ra provides a single numerical value that represents the average surface roughness, making it easier for fabricators to communicate specifications.
Calculating Ra
The formula for calculating Ra is as follows:
Ra = (1/n) * Σ|yi|Where:
- n = number of measurements
- yi = the deviation of the profile from the mean line over n sampling points
As such, a lower Ra value indicates a smoother surface, while a higher value corresponds to a rougher finish.
Surface Finish RMS (Root Mean Square)
RMS (Root Mean Square) is another important metric used to evaluate surface finish. It is similar to Ra but takes into account the square of the surface deviations. RMS is calculated by measuring the surface profile height and providing a more sensitive representation of surface roughness attributes than Ra.
Calculating RMS
The formula for calculating RMS is defined as:
RMS = √(1/n) * Σ(yi^2)Where:
- yi = the deviation of the profile from the mean line
- n = total number of sampling points
The RMS value typically tends to be greater than or equal to the Ra value, depicting the overall energy of the surface texture.
Key Differences Between Ra and RMS
While both surface finish Ra vs. RMS provide vital information about surface quality, they possess distinct features that set them apart:
- Measurement Basis: Ra is an arithmetic average while RMS is a quadratic average, making RMS more sensitive to larger deviations and peaks.
- Surface Representation: RMS tends to provide a better indication of the surface’s actual performance under operational conditions due to its sensitivity.
- Applications: Depending on the application, one metric may outweigh the other. For instance, industries focusing on fluid dynamics prefer RMS for its representation of surface interactions.
Importance of Surface Finish in Metal Fabrication
In metal fabrication, the choice of surface finish not only affects aesthetic values but also impacts functional capabilities. Considering factors such as wear resistance and lubrication, surface finish plays a significant role in:
- Reducing Friction: A finer surface finish leads to reduced friction when surfaces slide against each other, which is essential in engineering applications involving bearings and gears.
- Enhancing Corrosion Resistance: Smooth surfaces are less prone to corrosion as they hold fewer contaminants and allow for better protection against environmental factors.
- Facilitating Proper Sealing: In assembly processes, smoother finishes guarantee better seals and reduce the risk of leakage in critical components.
Guidelines for Choosing Between Ra and RMS
When determining the specifications for surface finish, fabricators should consider the following guidelines:
1. Understand Your Application Requirements
Assess the operational environment and performance requirements of the product. For example, precision components may necessitate a stricter surface finish standard, while aesthetic components might prioritize visual appeal over tactile smoothness.
2. Consult Industry Standards
Many industries have established standards that dictate acceptable ranges of surface finish. These standards can guide the decision on whether to use Ra or RMS.
3. Balance Cost and Performance
Finer surface finishes typically require more extensive processing, leading to higher costs. Fabricators must find the right balance between performance requirements and budget constraints.
Improving Surface Finish in Metal Fabrication
1. Choose Appropriate Manufacturing Techniques
Various manufacturing processes, such as machining, grinding, and polishing, directly affect surface finish. The selection of the most suitable technique can improve Ra and RMS values effectively.
2. Optimize Tooling and Equipment
Using high-quality tools and maintaining equipment can significantly enhance surface finish. Regular maintenance minimizes defects and allows for consistent output quality.
3. Implement Quality Control Measures
Regularly inspecting and measuring products during the fabrication process helps identify deviations early, allowing processes to be adjusted immediately to ensure the desired surface finish is achieved.
Case Studies: Ra and RMS in Action
1. Aerospace Industry
In aerospace manufacturing, surface roughness is crucial for reducing drag and improving fuel efficiency. Various parts such as turbine blades have strict requirements, often relying on RMS values to determine their effectiveness under high-speed conditions.
2. Automotive Application
The automotive sector focuses on balancing aesthetics with functionality. Here, Ra metrics may be prioritized during external body manufacturing to ensure a smooth, appealing finish, while RMS is closely monitored for internal components where performance is critical.
Conclusion
Understanding the intricacies of surface finish Ra vs. RMS is essential for metal fabricators aiming to optimize product quality. By selecting the appropriate surface finish metric based on application needs, adhering to industry standards, and implementing effective manufacturing practices, businesses can enhance their operational efficiencies and product performance. In the competitive landscape of metal fabrication, investing in the knowledge of surface finish characteristics and their impact on performance is a key differentiator for success.
surface finish ra vs rms